Key Takeaways
- The imposition of tariffs on some of the U.S. market’s major supplier countries are creating uncertainty for manufacturers.
- More than half of surveyed manufacturers plan to invest in advanced data analytics to help navigate tariff-related challenges.
- AI-enabled data analysis can help spot risks and opportunities in the manufacturing supply chain, helping manufacturers survive and thrive in a changing business landscape.
Building more resilient operations is always top of mind for manufacturers. But with the new U.S. presidential administration’s tariffs on some of the U.S. market’s major supplier countries, that resiliency may be tested. This is especially true for organizations without the technology in place to help them stay ahead of challenges and spot opportunities in a shifting business environment.
One of the most important areas where technology, especially AI tools, can help manufacturers maintain a firm grip on their profitability is data collection, analysis, and insights. Without the right data — and tools to turn it into actionable information — organizations will struggle to identify areas for improvement.
Better data means improved efficiency and productivity, potentially leading to cost savings. Manufacturers can gain these advantages by:
- Identifying inefficiencies in production
- Identifying which parts of the operation are best suited for reshoring/nearshoring
- Exploring alternative materials and suppliers
- Improving demand planning and forecasting (which is especially important as proposed tariffs affect buyer behavior)
But gathering, sorting, and analyzing all that data using manual processes can slow an organization’s ability to pivot to meet new changes. To build a more resilient supply chain, manufacturers need to quickly turn raw data into actionable insights that improve operational efficiency.
AI tools process information far faster than traditional processes, helping manufacturers future-proof operations against policy shifts, workforce trends, and geopolitical events.
Investing in Technology: A Path to Resiliency
According to a recent survey of 300 U.S.-based manufacturers and distributors by Eide Bailly and Manufacturing Dive's studioID, 94% of respondents plan to increase their technology and automation investments over the next three years. Over half (56%) of those surveyed plan to invest in advanced data analytics.
When seeking to establish more resilient operations, starting with data — and investing in technologies like AI to get actionable insights from that data — makes sense. Better visibility leads to a greater ability to aggregate information on supplier performance, equipment status, efficiency, and customer reviews. With the insights gained from that readily accessible and easily digestible information, manufacturers have powerful tools to help make their operations leaner, faster, and more agile.
AI can help manufacturers:
- Forecast consumer demand shifts that may occur due to tariffs' effects or other factors — and how to avoid negative impact. Considerations include higher operating costs due to tariffs and to what extent the organization may be able to absorb some of those costs to remain competitive.
- Optimize production line schedules to ensure the most efficient allocation of resources.
- Monitor machine usage time and maintenance schedules to avoid downtime from broken machinery and to schedule routine maintenance.
Supply chain resiliency depends on a range of factors that can be difficult to juggle with manual processes. By employing the right AI tools and applications, manufacturers can create a supply chain that can adapt to changing conditions, faster.
Want to learn how manufacturers are harnessing the power of data and technology to prepare for challenges in 2025 and beyond? Check out the 2025 Mid-Market Manufacturing Outlook survey report here.
2025 Mid-Market Manufacturing Outlook Report
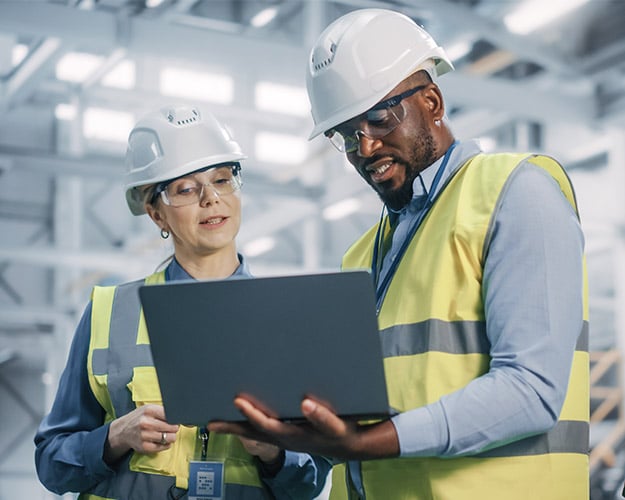
Manufacturing, Distribution, and Logistics
Rely on the trusted expertise of manufacturing advisors to help you build and execute your strategic vision.
Who We Are
Eide Bailly is a CPA and business advisory firm helping our clients grow, thrive, and embrace opportunities and innovation.
