Key Takeaways
- Efficient, responsive, and resilient supply chains give manufacturers a competitive edge in an increasingly complex and interconnected landscape.
- Manufacturers are turning to technology to address supply chain challenges, with 63% of manufacturers planning to update their existing technologies over the next three years.
- Enhanced supply chain visibility and resilience can empower manufacturers to quickly identify and respond to disruptions, mitigate risks, and facilitate more strategic decision-making.
Supply chain disruption can be devastating. One McKinsey study found that in most sectors, a single lengthened shock to production could wipe out up to half a year’s profits or more. To cope with current market trends and potential future challenges, manufacturers need to concentrate on their long-term supply chain strategy, with a focus on visibility and digitalization.
Good supply chain visibility and resilience are crucial for manufacturing organizations that want to ensure continuity of supply, operate more efficiently, and provide better customer service. And technology advancements have made these goals easier to achieve, giving organizations the tools they need to shield against unexpected disruptions, identify bottlenecks, mitigate risks, and make more strategic decisions.
Technology Enables Better Supply Chain Visibility
Manufacturers must accelerate technology adoption and prioritize data and analytics to gain visibility and foresight. Digitizing operations unlocks real-time data that leaders can use to make decisions about production regardless of circumstance. Smart supply chain design like smart logistics solutions, the Internet of Things, robotics, and artificial intelligence can shape operational effectiveness and enhance efficiencies.
Take, for instance, the role of AI in planning and delivery across the supply chain. Generative AI systems are perfect for automating manual manufacturing processes like ordering or target setting. Further, AI backed by solid data can provide insight into inventory trends, factory-floor production scenarios, or warehouse efficiency concerns.
Better data drives better business decisions. Learn more: AI-Enabled Data: A Manufacturer’s Secret Weapon for Supply Chain Resiliency
Our recent survey report shows manufacturers understand the connection between technology and resilience. Three hundred executives in various distribution and manufacturing sectors — such as food, metal machine and product, hi-tech, chemical, and process — provided insights. The survey found:
- Nearly half (49%) of manufacturers currently manage supply chain, logistics, and transportation challenges.
- Disruptions (52%), rising business costs (35%), and the pressure to digitize operations (33%) are their top challenges.
- About one in five (21%) manufacturers face limited supply chain transparency, and 45% say they’ve worked to improve their end-to-end visibility over the last year.
The survey reflected a clear trend toward digitization among manufacturers in the past year, with 33% working to digitize their supply chain management processes. Additionally, 45% of manufacturers optimized their inventory management strategies — a move that will help their organizations reduce long-term costs, avoid shortages, streamline inventory, and improve transparency.
- Read the full 2025 Mid-Market Manufacturing Outlook survey report to explore more findings.
Optimize Your Supply Chain
A more efficient, responsive, and resilient supply chain gives manufacturers
- Improved demand planning and forecasting
- Enhanced inventory management
- Increased operational efficiency
- Better risk management
- Stronger customer and supplier relationships
- Access to data-driven decision-making
- Cost reductions
Diversify Your Supply
Building a strong supply chain requires establishing relationships with multiple suppliers and manufacturers. More than 70% of supply chain leaders have already made changes to the size and number of locations in their supply chain network within the past two years. And 51% have increased the number of locations.
These findings illustrate the need to adapt networks to meet new market challenges. To secure your own supply chain, spread your procurement out so you’re not tied to just a few companies, especially for your most vital products and processes. You could have multiple suppliers of the same raw material so that, in a time of disruption, you can lean more on one than another.
Further, establishing cooperative relationships with multiple suppliers allows you to adjust your forecasts and orders and increase sales more easily.
Meet Challenges Head-On and Leverage New Opportunities
Looking ahead to the next three years, nearly all surveyed manufacturers plan to increase investments in technology and automation, and 49% plan to prioritize supply chain optimization.
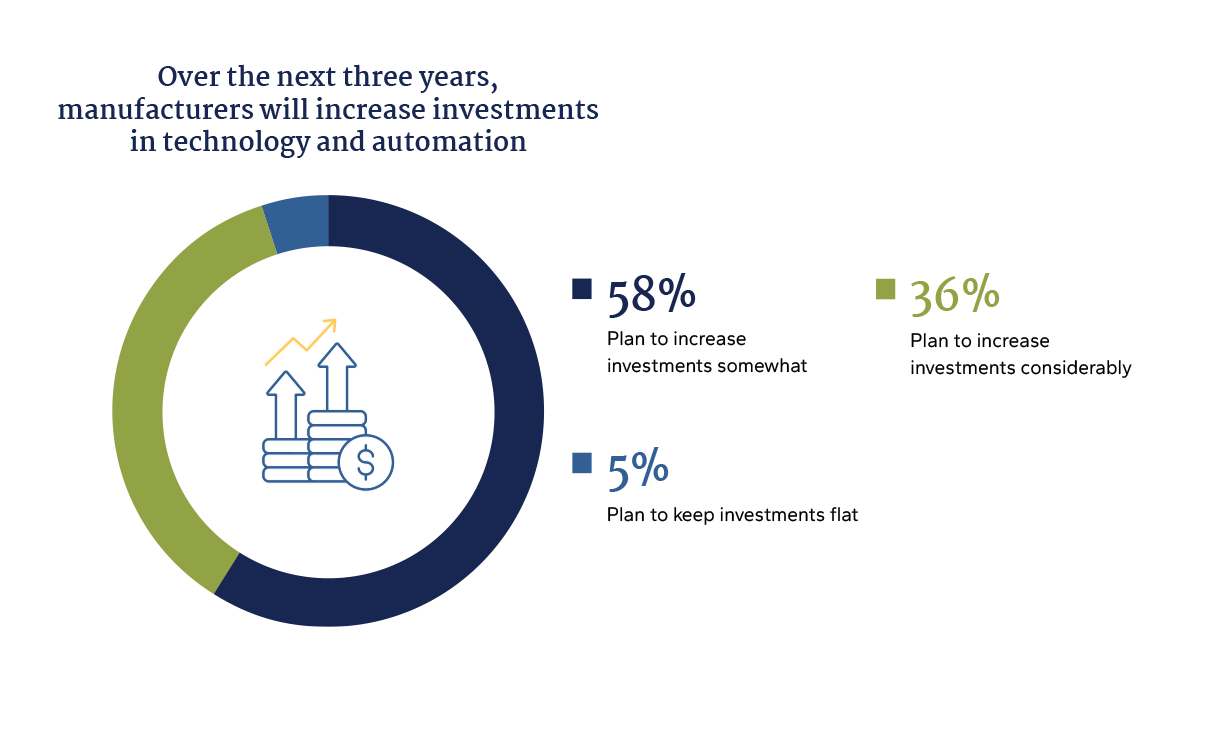
Ultimately, the success of any organization hinges on its ability to adapt, evolve, and consistently meet its customers’ needs. With the Internet of Things, artificial intelligence, supply chain management applications, robotics, automation, and other advanced tools at their disposal, manufacturers can improve supply chain visibility and resilience, navigate emerging challenges, and harness new opportunities.
But building a more resilient supply chain begins with planning. To achieve the visibility, agility, and traceability necessary, organizations must begin to implement supply chain optimization and planning. Every step in the supply chain process — from ordering raw materials to delivery — must be reliable.
Strategic, long-range supply chain planning involves the establishment of a framework for your supply chain. This includes a deep dive into your business and its suppliers with the goal of improving operations, standardizing processes, and planning for disruption.
Areas to review include:
- Demand planning
- Supply management
- Production management
- Inventory management
- Pricing strategy
- Event management
- Distribution planning
- Integrated business planning
By building these strategies into every aspect of your operation, you’ll be better prepared to meet disruption and fluctuating market trends head-on.
2025 Mid-Market Manufacturing Outlook Report
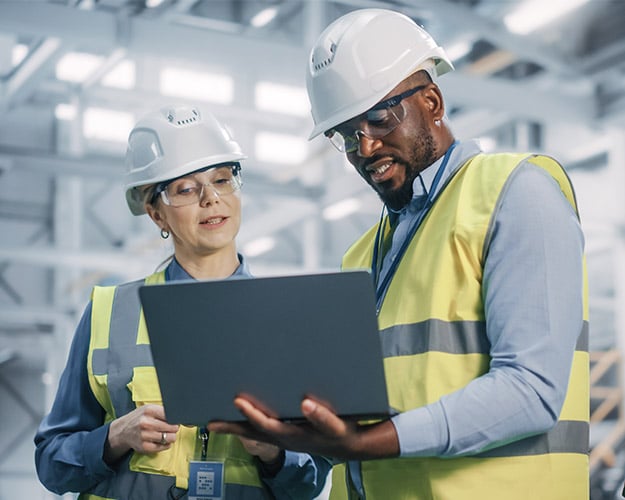
Manufacturing, Distribution, and Logistics
Rely on the trusted expertise of manufacturing advisors to help you build and execute your strategic vision.
Who We Are
Eide Bailly is a CPA firm bringing practical expertise in tax, audit, and advisory to help you perform, protect, and prosper with confidence.
