2025 Mid-Market Manufacturing Outlook
Discover how manufacturers are navigating challenges and seizing opportunities in 2025.
Access the Report Now2025 Outlook: Key Findings
Our survey of 300-U.S.-based manufacturers and distributors highlights how manufacturers approach business growth, their technology investments, and the workforce trends impacting their operations.
- 93%are optimistic about growth
- 49%are facing supply chain, logistics, and transportation challenges
- 85%expect production increases
- 94%plan to increase investments in technology and automation
Manufacturers have a particular knack for solving problems and recognizing potential issues before they boil over into larger challenges.
Dave Glennon
Partner and Manufacturing Industry LeaderEide Bailly

Optimizing Technology
Technology optimization and modernization is the key to increased visibility and supply chain efficiency. Ninety-four percent of manufacturers are increasing their investments in technology over the next three years.

Navigating Challenges
Manufacturers are facing increasing competition for skilled workers, leading to a greater emphasis on wages and benefits packages, workforce training, and DEI initiatives in the workplace.

Achieving Sustainable Growth
From adding new product lines and targeting niche markets to expanding into new geographic regions and exploring M&A opportunities, all respondents to our survey are confident in their organization’s ability to pursue growth opportunities.
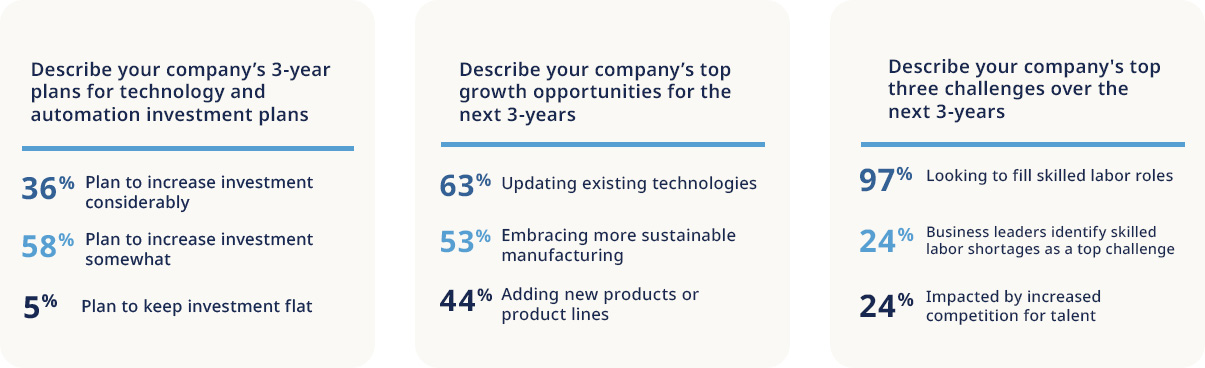
Explore Our Manufacturing Resource Library
Build a habit of sustained success.